トップCreating for TomorrowTomorrow’s Stories 旭化成が目指す水素社会、世界をリードする水素製造技術
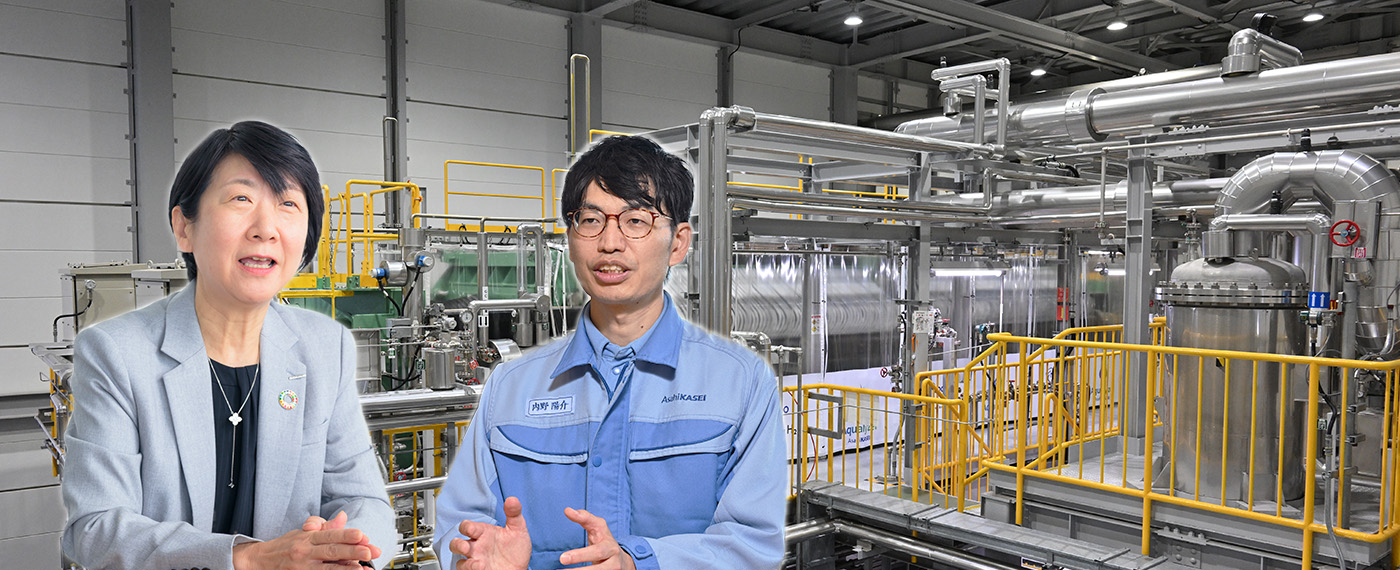
旭化成が目指す水素社会、世界をリードする水素製造技術
2023年10月31日
カーボンニュートラル社会の実現に向けて、次世代エネルギーとして世界中から注目を集める水素。本来無色透明であるこの水素は、製造方法や製造過程でのCO2排出量によって色で分類される。石油、天然ガス、石炭といった化石燃料をベースに製造し、その過程でCO2が排出されるグレー水素。排出されたCO2を回収・貯留して実質ゼロとするブルー水素。そして太陽光や風力などの再生可能エネルギーを利用し、水を電気分解して製造するためCO2を排出しないグリーン水素。脱炭素化にもっとも貢献できるのはグリーン水素であるが、その低コストかつ効率的な製造は技術的ハードルが非常に高い。特に実用化を想定した大規模・大量製造は、これまで世界でもほとんど前例がなかった。そんな中、旭化成はグリーン水素製造用の大型アルカリ水電解システムを開発し、事業化を目指す。世界をリードする水素製造技術で、水素社会の実現という壮大なテーマに挑む当社の想いとその取り組みに迫る。
Contents
水素社会の実現でサステナブルな未来へ
なぜ、水素が次世代エネルギーなのか—。その最大の理由は、エネルギーとして利用する際にCO2を排出しないという特徴にあり、世界中の国や企業、人々がCO2やメタンといった温室効果ガス削減によるカーボンニュートラルの実現に向けて動く中で大きな期待が寄せられている。また水素は軽くて広がりやすくスペースを要し、貯蔵・運搬には本来は不向きなのだが、水素を効率よく貯蓄・運搬する水素キャリアの技術研究も進んでおり、エネルギーとしての実用性も高まってきている。つまり、水素社会とは化石燃料を中心とした従来型の主要エネルギーをCO2排出量の少ない水素エネルギーに転換し、インフラ整備や経済面・技術面の課題を乗り越え、私たちの生活や産業において水素を使うことが浸透している社会を指す。それが、サステナブルな未来へとつながるのだ。
創業当時から紡がれてきた、グリーン水素製造技術
当社はカーボンニュートラル社会の実現に向けた新事業の創出を目指し、2021年にグリーンソリューションプロジェクトを立ち上げた。現在同プロジェクトでは、「CO2分離・回収・貯蔵(CCUS)」「バイオケミストリー」、そして「水素」の3つの領域で事業開発に取り組んでいる。中でも水素は注目度が高いテーマだ。
なぜ当社が、この水素事業に力を注ぐのか—。そこには約100年に及ぶ当社の歴史が関係している。1923年、宮崎県延岡市でアンモニア製造を開始した当社は、自社水力発電由来の電気で水素をつくり、アンモニアの原料として使用していた。再生可能エネルギーを利用して水素をつくる、グリーン水素製造の先駆けだったと言える。そこから半世紀、1975年には食塩水を電気分解し、塩素と苛性ソーダ(水酸化ナトリウム)を生産するイオン交換膜法食塩電解システムを事業化。現在世界の約160のプラントに食塩電解システムを供給し、イオン交換膜においては長年世界でも高いシェアを有している。
こうした歴史と脈々と伝承されてきた技術・ノウハウが、グリーン水素製造用のアルカリ水電解システムの開発に活かされ、当社独自の大きな強みとなっているのだ。各国政府や企業からの期待も大きく、グリーン水素製造はまさに当社ならではの強みを発揮してカーボンニュートラル社会の実現に貢献できる重要な事業と言える。
- 創業当時のアンモニア合成工場(水力発電の電力で作られた水素を活用)
若き化学技術者の情熱と挑戦
2015年、フランスのパリで開催されたCOP21※1において、温室効果ガス排出削減などのためにパリ協定が採択された。これを契機にグリーン水素が世界中で一気に注目されることになるが、当社は2010年にグリーン水素製造用のアルカリ水電解システムの開発を始めていた。
当社には食塩電解システムの事業経験を通して培われた工業電解のコア技術があったが、アルカリ水電解システムの開発自体は未知の領域。開発スタート時から技術者としてリードしてきた内野さんは、期待と不安が入り混じっていた当時の心境を話す。
「私は学生時代に化学を専攻し、その知識を活かして社会に貢献することを志して旭化成に入社しました。2007年にIPCC※2で地球温暖化の原因が温室効果ガスの増加と断定されてからは、特にその対策の分野で貢献したいという思いを募らせ、アルカリ水電解システムの開発への挑戦意思を社内で表明していたので、開発に参画することが決定した時はあまりの嬉しさから武者震いが止まらなかったことを覚えています。一方で自己の専門とは全く異なる世界に飛び込みましたし、必要なインフラが何一つ揃っていない状況でしたので、不安は大きかったですね。」
- 技術者としてFH2R実証に携わった内野さん
内野さんはアルカリ水電解システムの開発に参画する前までの数年間、電子部品の技術営業に従事していた。開発の推進にあたり、必要なインフラの整備・拡充を一から行う必要があったが、社内交渉においては前職で培った対話力と調整力が大いに活きたという。川崎、延岡、富士、水島といった各地に点在する研究・開発拠点間の協力関係を築き、技術知見やノウハウ、インフラを集結させることで開発の加速につなげた。そして2013年には、開発から2年半という短期間で現在の大型アルカリ水電解システムの原型となる中型実証機を開発。2015年にはNEDO※3事業を受託し、アルカリ水電解システムの大型化の検討に力を注ぎ、100kW級大型実証機での12,000時間という長期運転の通電実績を積んだ。さらにドイツのNRW州ヘルテン市に設立された「h2herten※4」に実証機を導入。これらの実績がNEDOから評価され、福島県の浪江町に建設された「福島水素エネルギー研究フィールド(FH2R)」におけるNEDO事業※5に、当社のアルカリ水電解システム「Aqualyzer™(アクアライザー)」が採用された。世界的にも有数の規模となる10MW級※6の大型アルカリ水電解システムの設計・開発に取り組み、建設・試運転を経て2020年より本格運用を開始した。
- ※1第21回国連気候変動枠組条約締約国会議(Conference of Parties)
- ※2気候変動に関する政府間パネル(Intergovernmental Panel on Climate Change)
- ※3国立研究開発法人新エネルギー・産業技術総合開発機構(New Energy and Industrial Technology Development Organization)
- ※4ドイツ連邦共和国NRW州ヘルテン市に設立された水素シティで水素関連技術開発拠点の一つ
- ※5水素社会構築技術開発事業/水素エネルギーシステム技術開発/再エネ利用水素システムの事業モデル構築と大規模実証に係る技術開発
- ※6最大運転時(毎時2,000Nm3)の消費電力
水素社会への歩みを進める浪江町、グリーン水素製造の現場
浪江町を巡ると、水素社会の幕開けを先取りして感じることができる。移動式の水素ステーションや道の駅に設置されている純水素燃料電池システムなど、さまざまな場所で水素がエネルギーとして導入・実証されているからだ。そして海岸沿いへ行くと、大量の太陽光パネルが一際目を引く「FH2R」が見えてくる。
- 福島水素エネルギー研究フィールド(FH2R)の全景 写真提供:NEDO
本NEDO事業におけるFH2Rの運用目的は、20MWの再生可能エネルギー由来の電力を用いた水素エネルギーシステムの実証である。その中でも当社への期待は、10MW級のアルカリ水電解システムによる水素製造の電力変換効率、長期信頼性、再エネ変動および系統ディマンドレスポンス指令への応答性の実証だ。
アルカリ水電解システムを用いた水素製造の最大の技術課題は、再生可能エネルギー由来の電力の変動対応である。従来型のアルカリ水電解システムでは、電力の変動に対する応答速度が遅い、起動・停止の繰返しの自由度が低い、また運転可能な電力変動幅が狭いため、再エネ変動に対応することが難しいといった問題があると考えられていた。これらは一般的に起動・停止の繰返しによる電力効率の悪化や、電力変動に伴う内部の流動状態の変化による構成部材の損傷が主な理由と考えられている。よって当社は、起動・停止に対して高い耐久性を示す部材の技術や、部材の劣化抑制のための保護回路の技術、内部流動の安定化技術など、変動に対応するための要素技術を開発した。それらの技術を駆使することで、長期間、グリーン水素を製造可能な大型アルカリ水電解システムを開発し、本NEDO事業での期待に応えることができた。
こうしてFH2Rでは3年間の実証運転を成功させ、「Aqualyzer™(アクアライザー)」は水素社会の実現という目標に向かって大きな一歩を踏み出した。
「10MW級の大型アルカリ水電解システムは、それまでの実証機と比較すると実に2桁近い規模であり、極めて挑戦的な実証だったと思います。担当技術者としては機器・部材を分解し、点検・評価する頻度を高めに設定し、ある程度デバックすることを見込みながら安定稼働を目指したいところでした。一方でFH2RでのNEDO事業はステークホルダーが多く、また水素の需要が高い期間もあり、簡単には水素製造を停止できない事情がありました。また実証期間が限られていたため、短期間でメンテナンスを行う必要もありました。そのような制約を乗り越えるために試行錯誤の末、デジタルツイン技術やビッグデータ解析技術を駆使した予兆保全の技術力を高めました。その結果、機器・部材を分解することなくトラブルの芽を未然に察知し、適切な対策を講じたため、安定稼働を実現することができたと思います。」
技術経営の世界では、研究から製品開発の難所を「魔の川」、製品開発から事業化の難所を「死の谷」と表現する。製品開発ステージでも多くの技術的な難題やトラブルを乗り越え課題を達成してきたが、FH2Rでの実証は失敗すると事業化の道が途絶える可能性もあり、まさにこうした表現に相応しい数々の難所があった、と内野さんは振り返る。
水素サプライチェーンを牽引する、旭化成の技術
現在グリーン水素製造の大型アルカリ水電解システムは、FH2Rでの実証を経て、2025年の事業化を目指してその取り組みを加速させている。FH2Rで得た知見やノウハウを活かしながら、電解性能の向上や水電解システムのコスト低減に向けてさらなる開発を進めている。また水電解システムだけでなく、遠隔監視による運転管理・予兆保全機能や、データドリブン(収集したデータをもとに運転を判断する手法)サービス、長期運用をサポートするメンテナンス事業を含めたトータルソリューションを提供するための開発も進んでいる。
加えて、水素社会の実現には社外とのさらなる連携が必要不可欠だ。グリーンソリューションプロジェクト長の植竹さんはこう話す。
「水素事業は川上のエネルギー供給企業や川中の水素運搬・貯蔵を担う企業、そして川下の水素需要家をはじめ、多くの企業と連携し、『つくる』『はこぶ』『つかう』の新たなサプライチェーンを構築する必要があります。ありがたいことに当社の大型アルカリ水電解システム『Aqualyzer™(アクアライザー)』に対する引き合いは多く、主体的にサプライチェーン構築を牽引しながら、最適なパートナリングを検討していきたいと考えています。将来的には水電解システムのリーディングサプライヤーとなることが目標で、2030年近傍には当社の新たな事業の柱の一つにしていきたいと考えています。」
- グリーンソリューションプロジェクト長の植竹さん
トラック、バス、鉄道、船舶、航空機などのモビリティ、化学や鉱業・建設業などの産業、そして私たちの生活……。人類に欠かすことのできないエネルギーが水素に転換されていく水素社会。そこに向けて考えなければならないことも、乗り越えなければならない課題も、まだまだ先が見えないほど山積みだ。それでも自分たちの仕事と今後の展望について楽しそうに語る2人の姿は印象的だ。「私たちのグリーン水素製造技術で世界を変え、サステナブルな未来を自らの手で築いていく」という大義と、そんな未来に向けて一歩ずつ確実に前進しているという実感が、この水素事業に携わるメンバーを突き動かすエネルギーとなっている。
- ※肩書・記事内容は取材当時のものです。